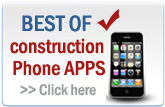
Ned Pelger's blog on construction, design and other weirdness. Email him at ned@constructionknowledge.net
Please help him win his readership competition against his son Lex at the Construction Phone Apps Blog
I love the 1932 photo of New York construction workers lunching on a beam. Due to the collaborative nature of Wikipedia, we now know much more about the photo. It was taken by Charles C. Ebbets during construction of the RCA Building (renamed as the GE Building in 1986) at Rockefeller Center. Ebbets took the photo on the 69th floor of the RCA Building during the last months of construction. It appeared in the Sunday photo supplement of the New York Herald Tribune.
Most of the men in the photo have been identified by relatives or descendants in the last few years. Though the identities of a few of the men are disputed (i.e. several folks claim him to be the person they know), most of the men are now known. As I read through the list, I’m fascinated by the number of immigrants. Ireland, Newfoundland, Sweeden and Slovokia are all represented. One of the men is a Native American from the St. Regis Mohawk Reservation.
So when you hear someone complaining about the number of immigrants working in construction, remember that the tradition goes way back. Our industry rewards skill, creativity and hard work. The employers who discriminate find themselves with less options (meaning less work) than those who embrace merit, whatever it looks like.
I challenge you (and me) to examine ourselves and think about our latent (or not so latent) prejudices. Can you afford them and do you really want them? You get to choose the kind of person you want to be.
I appreciated RB’s comments on my last post. Since the many documents needed on a jobsite tend to be digital anyway, why can’t we take the next step and just look at them on our mobile devises? Carol’s Construction Technology Blog addresses this issue and reports some huge productivity gains. She mostly discusses using the invoice approval and accounts payable system as a fully digital (that is to say, paperless) process. Apparently, dual computer monitors make the process much easier for accounting staff.
I’m going to challenge myself to learn how I could move my own job costing and invoice approval to a digital process. As I think about it, I believe I could save substantial time and aggravation, if I go through the work to make the change.
The joists in my garage that now strain under the weight of more paper files would probably appreciate the change.
Now’s the time to be evaluating these type options. But make sure not to just digitize an inefficient paper process. Think about what information really makes you smarter. Focus on the things that really help you and your co-workers to better build your projects. Let’s make changes that up our game. Remember, modern project management requires us to do more, better, faster and for less. It’s your chosen profession.
I read an ENR article about some design flaws in the World Trade Center NYC projects adding millions of dollars to the cost. I’m always curious about how those type problems arise and get resolved.
Apparently One World Trade Center will be a 104 story tower developed by the Port Authority of NY and NJ. The future Manhattan skyline is shown below. As the construction nears completion, they realized that a temporary subway station blocks the access for the loading docks into the new building. So temporary loading docks must be built (at a cost of several million dollars) that will be used until the temporary subway station can be dismantled.
Of course, no one takes full responsibility for those type of staging scenarios (and I know they are dreadfully easy to miss) and the taxpayer simply pays more. As I read more, though, that trend seemed to intensify.
The cost for the project increased by 22% to $3.8B USD. A $700M increase in times of almost no inflation seems another bitter pill for taxpayers. One World Trade Center is only 60% leased and the developer struggles to find tenants. Other related buildings in the World Trade Center complex also aren’t finding tenants and the scope of the projects, including the # of stories being built, are getting reduced.
I understand the complexity of deciding the right thing to build. When private developers make those decisions, they risk their future financial well-being on the results. The intensity (and often effectiveness) of their efforts increases as the real possibility of financial ruin looms. While America’s lenient bankruptcy laws allow private developers to take big risks without worry of sending their families into complete destitution, the pain of bankruptcy still deters.
Government entities as developers simply don’t face the same downsides. The decision makers may care intensely, but in the end the agency survives and everyone generally still has their jobs.
In my early days in construction, I remember a couple of my bosses telling me stories that made a surprising point. A bid was won that they later discovered had a substantial downside error. There was a debate about throwing in the bid, but a decision made to just live with the numbers and manage it as intensely as possible. Often those sure-fire financial loser projects turned into winners because every detail was managed so well.
I believe in the efficacy of intense construction management. I believe private entities have a much higher likelihood of managing construction projects with intense levels of efficiency. I guess that’s why I’m a private market enthusiast who owns my own business and encourages other like-minded folks to give it a try.
When we make expensive mistakes (which we all do) at least we tend to learn from them.
Having my own construction business was never really a dream of mine. I knew my wife’s concern for security and believed that she simply wouldn’t be able to live with the perceived risks. Then again, I never really did much long range planning in my life. I thought hard about what I wanted to do that day, that week and even that year, but never planned beyond a year. With all the variables involved, planning beyond a year just seemed (and still seems) like a waste of effort.
But November of 1995 suddenly lined up a few elements in my life. For the first time in years, I wasn’t that engaged in my job. I’d come through a serious illness and had re-evaluated life priorities. The concept of failure didn’t seem as scary. We didn’t have much money, but TBW believed in my capabilities. I was reasonably sure that if I failed, I could get some one to hire me to do something that would keep the family in food and the donkeys in hay. The economy was just coming out of a recession…in fact, a recession stemming from financial institutions over-lending.
So I jumped into my own business with no work lined up and the jobs came in a trickle, then a steady flow. I’ve never regretted the move and can’t imagine going back. A number of friends are contemplating making their own jump and feeling that same pressure. Here are 5 reasons I believe the Spring of 2012 is a great time to start your own construction business.
Good luck and Godspeed. By the way, expect a bit of a blip from the Euro crashing and burning, but I don’t believe that’s going to kill our recovery in the USA.
Houston Neal at the Construction Software Advice website pulled together a survey to gather data on construction estimating. The 2012 Construction Estimating Benchmark Survey does an excellent job of making you think about how you estimate projects and how your estimating process works.
Since estimating costs matters so much in construction, it’s worth ten minutes of your time to do the survey. Neal will send you the results, which should also provide some valuable info for most of us. Even if you’re not primarily an estimator, please take the survey. Thanks.
Last week I got an email from Jewel Cameron. He wanted to join the Construction Knowledge mailing list and told me a bit about himself. He’s from Guyana and has 25 yeas of practical construction experience there. I thought, “That sounds fascinating” and asked him to provide some details about building in Guyana. He obliged below.
I appreciated Jewel’s comments and hope he continues to build his career in this great industry of construction. As I looked for photos of Guyana in Google images, the one below made me think of some construction challenges they encounter that I’m glad to forego.
My friend Kneal sent me this construction site video that had me laughing out loud. If you work in or around construction, I guarantee you will laugh if you watch. A warning, though, you may find some of the language offensive.
httpv://www.youtube.com/watch?v=7KvxOuC7Bhc&feature=youtu.be
Hope you have a day where laughter invades your life. Remember, the first 100 years is the hardest.
I have a guest post blog today on a boring topic. Yet we should all understand the basics construction bonds, just to better understand our business.
When a project owner asks if you can bond the project, do you understand the question? Generally government projects require bonds (and occasionally private projects). The most commonly required surety bonds are payment and performance bonds. While they are two separate bonds that serve different purposes, they are usually acquired jointly.
Definition of Surety Bonds
Surety bonds are an agreement, or contract, between three parties. Each surety bond offers unique protections that, if not upheld, a claim can be filed upon the purchaser of the bond.
The parties involved in surety bond relationships are:
An obligee: the entity that is requiring the bond, typically a government organization
A surety: the agency providing the bond that ensures the principal will fulfill the work as specified by the bond
A principal: the business or person purchasing the bond
Background of Payment and Performance Bonds
The Miller Act, which requires bonds on federal construction projects with contracts exceeding $100,000, served as the foundation for surety bonds. Shortly following its passing several state legislatures adopted the act’s theory and deemed their requirements “Little Miller Acts.” Due to this, state bonding requirements vary from one area to another.
After the Miller Act’s passage, the Federal Acquisition Regulation was enacted which required payment bonds and performance bonds on contracts over $150,000.
Definition of Payment bonds
Payment bonds provide guarantees that all involved on a project will be fully compensated in the event the contract is voided or broken. Subcontractors, suppliers, laborers and materials are a few examples of those protected by payment bonds. Should a contractor default, those safeguarded by payment bonds will be compensated by the surety agency who wrote the payment bond. Following this, the surety will then seek retribution from the contracting organization who purchased the bond.
Definition of Performance bonds
Performance bonds, on the other hand, refer more to protecting the clauses within the contract. A performance bond is typically required from federal and state governments for work on public projects. The types of protections performance bonds ensure vary from one area to another, but typically refer to how a building is constructed, or the time in which the project should be completed by.
Surety Bond Cost
The most commonly asked questions regarding surety bonds are, often times, centered on their cost. Unfortunately, there is not one set cost of surety bonds, nor is there a set rate. Rather, surety bond rates work similarity to how credit rates are set for individuals. Several areas must first be researched before a final quote and price can be delivered to customers. These include: an individual’s financial history, the type of bond, and the surety’s policies.
Although rates can vary from one applicant to another, standard market rates are typically anywhere from 1 to 3 percent. Bad credit programs are available for high-risk applicants who have weaker financial backgrounds than others. These applicants typically pay higher rates between 5 to 20 percent of the bond amount.
In specific to payment and performance bonds, other items are investigated before supplying a bond. Surety agents will research the industry the surety bond is being written for, as well as where the bond is required. As surety bond requirements vary from state to state, rates can also fluctuate depending on how risky the project may appear and how many bonds are required in order to begin a project.
For financially stable applicants, typical costs (for contracts $1 million and under) can range between 1.5 and 2 percent of the contract amount. Also, bond costs decrease with the size of the bond. This means applicants may pay less than 1 percent of the contract price for performance and payment bonds on large-scale projects.
My friend Kneal sent me this fascinating link about the Global Village Construction Set. It’s an open source collaboration which will result in fabrication plans for 50 construction, industrial and farming machines. Focused on cost and energy effectiveness, tools such as tractors with backhoe and loader attachments, compressed earth brick presses and welders can be made in a poor village. These tools will help transform the economy, allowing businesses to build, grow and create wealth. I love the concept. Watch this short video to get a better understanding.
httpv://www.youtube.com/watch?v=CD1EWGQDUTQ
Just imagine building a compressed earth brick press and helping your neighbors build solid houses and factories. At 16 bricks per minute (5,000 bricks per day), an entire house can be created in one day with one operator using onsite soil materials. The construction cost for this type houses promises to be about $5/sf. Of course, when considering the energy embedded in the construction materials, including manufacturing and transportation, this product looks even better. As an aside, I think the energy embedded in construction will become a much bigger issue in coming years.
With these 50 machines available to Third World locations, the barriers to sustainable human settlements will be substantially lowered. In human terms, less children will die, more will become educated and able to fulfill their God-given potential.
If you’re a tinkerer, consider getting involved to support this Global Village Construction Set initiative. It might just change your life…as well as the lives of lots of children around the world. If you have any interest in this topic, definately watch the following TED video, it’s motivating! If this idea is truly sound, then the implications are significant.
If you know you could perform your job much better, but aren’t going to for your (pick one) jackass boss, low wages or company that promotes idiots, then you shouldn’t start a construction company. Customers are harder than all the above annoyances. The folks that excelled for their previous bosses tend to do well in their own firm. The complainers, malcontents and brilliant guys that won’t waste their efforts without appropriate rewards go bankrupt.
If you can’t manage your personal finances and are always on the verge of fiscal ruin, then you shouldn’t start a construction company. The same self control that allows folks to make their ends meet in tough situations cause prosperity in business.
If you are a liar, a chisler or a theif, you shouldn’t start a construction business. In a small business, reputation rules. The poor character and bad moral choices you made in your previous jobs probably won’t change when you run your own business. What will change, though, is that others can much more easily avoid you. Word spreads quickly about bad behavior and no one has to use your firm. In short, good character pays.
So, it’s a great time to start thinking about your own construction business, but not for the knuckleheads described above.