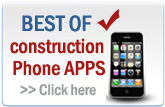
Ned Pelger's blog on construction, design and other weirdness. Email him at ned@constructionknowledge.net
Please help him win his readership competition against his son Lex at the Construction Phone Apps Blog
I read a fascinating article this morning in ENR titled Inconvenient Truth: Pittsburgh LEED Gold Building Energy Hog. The article begins as follows:
A first study of the David L. Lawrence Convention Center’s “green building” features has uncovered a quirk in its electrical system that has cost taxpayers $70,000 to $100,000 a year in wasted-power penalties charged by Duquesne Light Co. since 2003.
Known as a “power correction factor penalty,” the extra charge shows the 1.5 million-square-foot center does not run as efficiently as possible and that wasted electricity accounted for 6 percent to 8 percent of its yearly bill, which was $1.27 million in 2010.
“It is wasted energy in a sense,” said Steven Musial, an electrical engineer at CJL Engineering in Moon. “It’s like the foam on a head of beer. A lot of foam is not desirable. It doesn’t do anything for you. The power isn’t in the foam; it’s in the beer.”
The $373 million center’s website touts its LEED Gold rating from the U.S. Green Building Council and includes the slogan “Built Green. Working Green. Every day!” LEED stands for Leadership in Energy and Environmental Design, and the rating is a measure of how efficiently it uses water, electricity and other resources.
The Pittsburg Convention Center’s power factor varied from 0.65 to 0.85, while an acceptable power factor is generally around 0.95. They solved the problem (8 years later) by installing two large capacitors for about $300k.
Initially, I smugly considered how stupid the LEED standard was, then I considered how the buildings I’ve built do regarding their power factor. Truth is, I don’t know. None of the owners I’ve worked for have ever brought it up as a concern and I’ve never checked. I understand the theory of the power factor, shown in my sketch below:
Yet it isn’t something I think about during the design and installation of the electrical system. And I’ve never poured over electric bills from finished projects to see how they perform.
Unfortunately, many items get decided during the design and construction of buildings, but the assumptions don’t get verified and checked during the building operations. Does anyone else have a way that this scenario works? Do you follow up and determine how your buildings actually work?
Seems like there’s an opportunity in there somewhere, though I’m not quite sure how to grab hold of it.